Testing 1, 2, 3 - The History of Speaker Testing and Best Practices
Although the foundational concept of a loudspeaker has not changed drastically in the last century—still consisting of a voice coil, magnet, and cone—the development of novel materials and acoustic engineering methods has accelerated progress. For instance, engineers now experiment with specialized cone materials like Kevlar, carbon fiber, and advanced cellulose composites to tailor frequency response and durability. Magnet technologies have also evolved, using neodymium and other alloys to increase power density while reducing weight. Modern measurement techniques have enabled significant refinements by offering deeper insights into transducer behavior and enabling iterative improvements early in the design cycle.
Anechoic Chambers and Early Testing Methods
During the 1930s, anechoic chambers offered a groundbreaking solution for measuring loudspeakers in an environment free from reflections. At that time, engineers employed a slow-swept sine wave from an oscillator, with a strip chart recorder documenting the output. Rotating the speaker manually to achieve various measurement angles was labor-intensive and vulnerable to operator error, especially since maintaining a consistent orientation for each test point could be difficult. Additionally, small vibrations or minor placement shifts could skew the data, underscoring how precision and repeatability were early challenges in speaker testing.
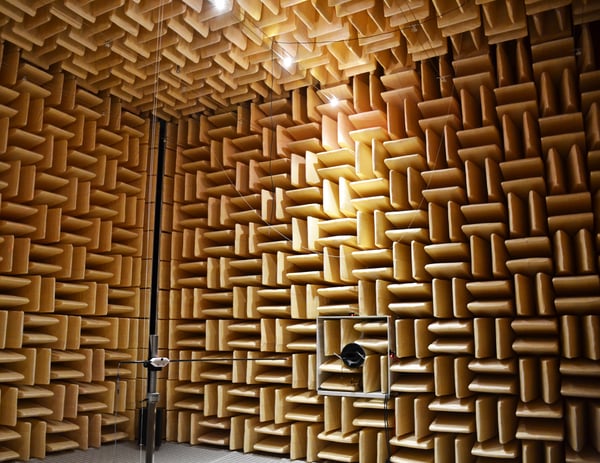
Computer Revolution in Speaker Testing
By the late 1960s, time delay spectroscopy and Fourier analysis began to reduce reliance on massive anechoic facilities. Greater accessibility to computational resources in the 1980s led to increased measurement speed and accuracy. Over time, industry guidelines evolved to require a full 360° data set, providing an expanded view of how loudspeakers radiate sound in real-world conditions.
Klippel Near Field Scanner Takes it to the Next Level
The Klippel near-field scanner (NFS) platform represents a major breakthrough in transducer evaluation. Using holographic analysis in the near field, it reliably extrapolates far-field performance without the need for anechoic conditions. After the system is set up and programmed, it collects thousands of data points automatically in just a fraction of the time older methods require. Beyond capturing key performance metrics like linearity and thermal stability, it quantifies distortion and power handling. Because near-field measurements can reveal subtle phenomena that might go unnoticed in a larger chamber, the NFS can pinpoint issues related to driver asymmetry, motor nonlinearity, and small-scale cone resonances. This method is particularly advantageous for optimizing both large and small drivers, including those operated in vacuum chamber scenarios, because it eliminates the need to physically rotate and reorient each sample.
State-of-the-Art Testing at MISCO
Warkwyn, MISCO’s testing division, maintains one of the most advanced independent Klippel labs in North America and also serves as the North American distributor for Klippel systems. In addition to Klippel analyzers, MISCO integrates other diagnostic solutions:
- SoundCheck by Listen, Inc. for end-of-line quality control. Beyond simple pass/fail checks, the system can be configured to measure frequency response, phase, and distortion at production-level speeds.
- True Technologies’ automated Life Test to determine power handling under both short- and long-term stress, allowing engineers to correlate thermal and mechanical fatigue data with real-world usage.
- LPM and LSI modules to assess linear and non-linear parameters, 3D displacement, and harmonic distortion. This data illuminates how a loudspeaker performs when driven hard, revealing whether the motor assembly or suspension can handle extreme excursions.
- Suspension Part Measurement (SPM) to evaluate the dynamic motion of the surround and spider. Minute changes in spider geometry or stiffness can alter the speaker’s resonant behavior and excursion limits.
- Material Parameter Measurements (MPM) to quantify properties such as Young’s Modulus. This helps engineers select materials that provide the right combination of stiffness, damping, and longevity.
- Laser Scanning Vibrometer (SCN) to visualize vibrational modes throughout the audio spectrum, pinpointing areas on the cone or surround that may cause unwanted resonances.
Ongoing Advancements
Speaker measurement protocols are constantly evolving, often propelled by emerging technologies. MISCO is dedicated to staying at the forefront of these advancements, ensuring each transducer meets stringent performance requirements. Although the discipline can be intricate, MISCO is always ready to recommend the right level of testing to match a project’s unique demands, prioritizing the parameters most pertinent to each application.
Partnering with Experts for High-Performance Loudspeaker Solutions
Achieving the best possible audio outcomes calls for collaboration with a trusted partner who comprehends the nuances of loudspeaker design. Drawing on more than 75 years of experience, MISCO has built a reputation for designing and manufacturing robust, high-performance loudspeaker systems.
Whether we’re creating a custom audio solution for a specialized project or recommending an existing design, our commitment to excellence remains constant. Every product undergoes a rigorous inspection to meet stringent quality standards. By leveraging advanced technologies like laser scanning and performing thorough end-of-line tests, we ensure that your loudspeakers will excel in demanding applications.
If you seek a partner to help you develop superior loudspeaker solutions, reach out to MISCO. Our team is ready to collaborate and deliver the tailored results you need.