Why Thermal Management is Crucial for Loudspeaker Voice Coil Performance
Like many mechanical and electrical devices, loudspeakers generate heat that needs to be dissipated. If left unaddressed, it could lead to many issues.
Loudspeakers are remarkable instruments that rely on electricity, magnets, air pressure, materials, and many other factors to produce sound. If any one of these elements is altered in a loudspeaker, it can result in an unintended sound or perhaps no sound at all. The voice coil is at the heart of a loudspeaker; without it, a loudspeaker doesn't operate.
When connected to an audio source, a moving coil loudspeaker, the most widely used and commonly known form of loudspeaker, turns its voice coil into an electromagnet with alternating polarities. The voice coil interacts with a permanent magnet with fixed polarity, causing an in-and-out motion. This movement drives the loudspeaker's diaphragm, pushing and pulling air to create sound waves.
An important thing to know about the voice coils in loudspeakers is that they are not very efficient. Generally, they are only about 3-5% efficient, meaning that if you put 100 watts of power into a loudspeaker, you will only get 3-5 acoustic watts of sound output. The remaining energy is dissipated as heat, causing the voice coil to become very hot during normal operation. A significant amount of heat is produced during standard operation, making effective thermal management crucial in loudspeaker design and material selection.
The Role of Wire Material in Voice Coil Heat Management
A voice coil in a woofer playing music at high volumes for just a few minutes can easily reach temperatures of 200 °C. When heat is not efficiently dispersed, the voice coil's resistance increases significantly, potentially doubling. This rise in resistance reduces the loudspeaker's sensitivity and performance, leading to diminished sound quality.
The most effective way to manage this heat is by carefully selecting the materials used to construct the voice coil. The coil wire and the former (also called the bobbin) are two critical components that influence thermal performance. The coil wire carries the electrical current that generates the electromagnet and is wound around the former, which provides structural support. Since the coil wire generates heat during operation, both it and the former must be made from materials that can withstand high temperatures and efficiently dissipate heat.
A common material choice for coil wire is copper, primarily due to its excellent electrical and thermal conductivity. Copper effectively conducts electricity, which is essential for generating the electromagnet fields in the voice coil, and its good thermal conductivity helps dissipate heat generated during operation. Copper-clad aluminum wire is another popular option; it combines copper's high conductivity with aluminum's lightweight properties. This material is often used in applications where reducing the moving mass of the loudspeaker is essential for performance.
When considering thermal management, it's important to note the temperature coefficient of resistance for these materials, which indicates how much the electrical resistance changes with temperature. Copper has a temperature coefficient of resistance of approximately 0.386% per degree Celsius, meaning its resistance increases by that percentage for every degree Celsius rise in temperature. Aluminum is close behind, with a coefficient of about 0.429% per degree Celsius. A higher temperature coefficient means that the material's resistance increases more with temperature, which can affect the loudspeaker's performance if not properly managed.
Formers and Their Role in Voice Coil Thermal Resilience
After considering the material of the coil wire, the next crucial component to address for heat handling is the former. The former gives the voice coil its structural support and is commonly made from materials such as paper, aluminum, fiberglass, or polyimide film (best known by the brand name Kapton). The choice of the former material significantly impacts the voice coil's ability to withstand and dissipate heat during operation.
Fiberglass and Kapton are more commonly used among these materials due to their superior heat resistance and durability. Fiberglass is highly durable and heat-resistant, capable of withstanding continuous operating temperatures up to approximately 537 °C and not melting until it reaches around 1,482 °C. Kapton is also known for its excellent thermal resilience, handling temperatures up to 260 °C without degrading. Although Kapton has a lower maximum temperature rating compared to fiberglass, it offers advantages like lighter weight and flexibility, which can be beneficial in certain loudspeaker designs.
In contrast, materials like paper are less heat-resistant and may degrade under high-temperature conditions, while aluminum formers, despite their excellent thermal conductivity, can introduce undesirable electrical effects like eddy currents. Therefore, selecting the appropriate former material is essential for managing heat and ensuring the longevity and performance of the loudspeaker.
Other Key Design Factors in Loudspeaker Heat Management
In addition to material selection, several other factors can effectively manage the heat generated by a loudspeaker. The voice coil's size significantly impacts heat dissipation; larger voice coils have more surface area, allowing for more efficient heat transfer and reducing the risk of overheating. The type of adhesive used to bind the voice coil components can also affect heat dissipation. Though their impact on heat dissipation is relatively minor compared to other factors, using high-temperature adhesives ensures the structural integrity of the voice coil under thermal stress.
The overall design of the loudspeaker is another crucial factor in managing heat. A thick top plate can help dissipate heat by acting as a heat sink, drawing heat away from the voice coil. However, it may also affect the acoustic characteristics of the loudspeaker by altering the magnetic flux density (the strength of a magnetic field) and adding mass, which can influence the loudspeaker's responsiveness. The alignment of the voice coil and magnet to facilitate airflow around them is also vital; efficient airflow aids in cooling through convection.
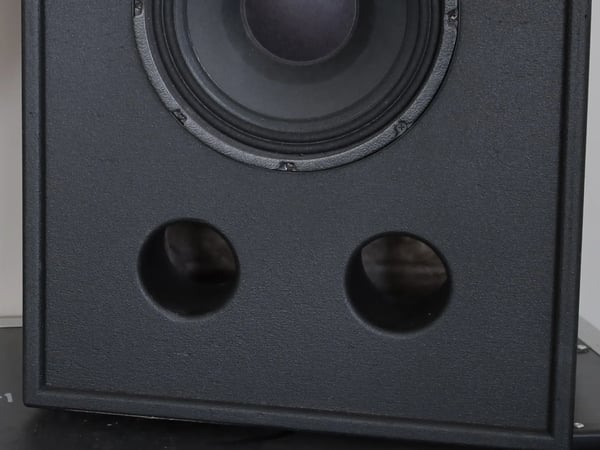
Additionally, the loudspeaker enclosure impacts thermal management. Factors such as the materials used for the enclosure, the presence and type of internal damping materials, the inclusion of ports, and the placement of these ports all affect airflow and heat dissipation. Proper ventilation and airflow within the enclosure can significantly enhance heat dissipation. All these aspects must be considered when designing a loudspeaker to avoid overheating and ensure optimal performance.
Designing a Loudspeaker
Of course, the thermal management of voice coils is only one of many things that need to be considered when designing a loudspeaker. Partnering with loudspeaker engineers who have a deep understanding of all the necessary components—and the ability to conduct comprehensive testing—is what separates generic loudspeakers from well-crafted ones that sound great and can last decades.
MISCO not only offers comprehensive engineering services but also manufactures loudspeakers right here in the United States. We have complete control over the manufacturing process and are known for the reliability of our products, thanks to superior design and stringent end-of-line testing. Additionally, MISCO provides a full catalog of off-the-shelf solutions to help our customers save money on their projects.
If you're looking for high-quality loudspeakers for your next project, contact MISCO today. A member of our team will help you select the right loudspeaker solutions to meet your specific needs.