3D Printing Applications in Loudspeaker Manufacturing
3D printing has become a game-changer for many industries, and loudspeaker OEM manufacturers are no exception. This technology saves time and money by enabling rapid prototyping and reducing the need for costly tooling, helping manufacturers to innovate faster, more efficiently, and in entirely new ways. From cutting development costs to customizing products quickly, 3D printing offers several key advantages that make it an indispensable tool in modern loudspeaker development.
The Rise of 3D Printing in Loudspeaker Design
While 3D printing has existed for several decades, it has now become a mainstream technology for producing finished products and specialized prototyping. Its widespread adoption is mainly due to its significant time and cost savings compared to traditional manufacturing methods, such as designing and tooling molds. Advances in printing technology and a reduction in the cost of 3D printing have also contributed to its mainstream adoption, making it accessible to more manufacturers. By eliminating these time-intensive steps, manufacturers can innovate faster and readily adapt to changing needs.
Traditional Methods vs. 3D Printing
Traditional methods of designing and creating molds are labor-intensive and expensive. They often require specialized equipment and significant manual effort to produce each mold. The process involves crafting a custom mold for each component, necessitating precision machining and tooling. Each mold must be tested and adjusted for accuracy; even minor design changes can force a complete restart of the process. As a result, this leads to considerable increases in time and cost, often taking weeks or even months for each iteration.
In contrast, 3D printing eliminates the need for molds, allowing manufacturers to quickly transition from concept to functional prototype. Design changes can be directly implemented in the digital model, drastically reducing iteration time. Modifying designs on the fly without retooling helps save weeks or even months in development time, making 3D printing a more efficient alternative to traditional methods.
Demystifying the 3D Printing Process in Loudspeaker Manufacturing
The process begins with an engineer using specialized software to design parts and components on a computer. These designs are saved as STL (Standard Tessellation Language) files, which are 3D models that detail the object's geometry.
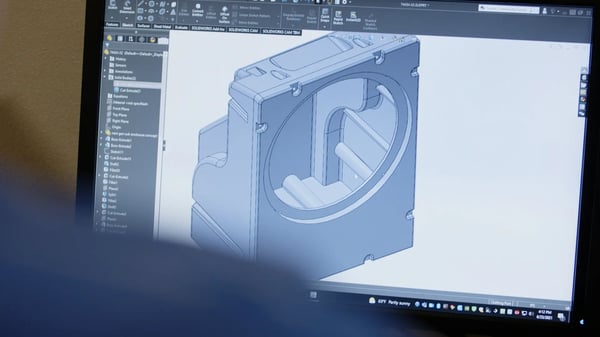
Next, these STL files are converted into G-code files. G-code contains the precise instructions that direct the 3D printer on how to move, layer by layer, to create the physical object. This process is similar to how an inkjet printer receives instructions to print a 2D image; however, in this case, it builds a complex three-dimensional structure.
Guided by a computer, the printer constructs the object layer by layer using thermoplastic or fused powder as "ink." This additive manufacturing process results in three-dimensional objects that can be tested and refined before moving into full production.
This design-to-production workflow ensures that each prototype is highly accurate and meets the desired specifications. It also allows for rapid iterations without the cost of creating new tooling for each version.
Benefits of 3D Printing in OEM Loudspeaker Development
3D printing has many advantages in OEM loudspeaker development, including rapid prototyping, complex geometries, customization, material innovation, cost efficiency for small production runs, and environmental benefits.
- Rapid Prototyping
-
Rapid prototyping is one of 3D printing's most significant advantages for OEM loudspeaker manufacturers. It enables quick production and testing of physical prototypes, allowing for fast design iterations. Adjustments can be made directly to digital models without tooling, significantly reducing development time and costs compared to traditional methods. This efficiency helps manufacturers adapt quickly to design changes and swiftly bring products to market.
- Complex Geometries
-
With 3D printing, OEM manufacturers are no longer limited by traditional design constraints, allowing them to create highly specialized enclosures for a variety of applications. This includes designing intricate and optimized shapes that enhance acoustic performance for soundbars and satellite loudspeakers, which are often integrated into products like casino gaming machines, kiosks, or appliances.
Satellite loudspeaker in a 3D-printed enclosure. Developing complex geometries enables manufacturers to create internal bracing structures that reduce resonance and improve sound dispersion without adding unnecessary weight or cost. For example, designing enclosures for integration into gambling machines requires compact yet efficient sound solutions, which 3D printing makes possible. By moving beyond the standard boxy enclosure, manufacturers can create innovative designs that meet specific spatial constraints and performance requirements while ensuring aesthetic compatibility with the overall product.
- Customization and Flexibility
-
3D printing provides a high level of customization, enabling manufacturers to meet specific customer requirements with precision. Manufacturers can design unique loudspeaker enclosures optimized for aesthetic appeal and acoustic performance. The ability to rapidly modify designs without costly tooling allows for personalized solutions that efficiently meet individual needs.
- Materials
-
The materials used in a loudspeaker enclosure significantly affect its acoustic performance, and 3D printing provides the flexibility to explore a broader range of materials than traditional methods allow. Different 3D printing materials have distinct impacts on how a loudspeaker enclosure functions:
- Thermoplastics
-
Thermoplastics are commonly used for enclosures because of their lightweight and durable properties. They allow manufacturers to control rigidity and resonance, which directly affects sound quality. By adjusting the rigidity, manufacturers can change the enclosure's resonance, influencing how sound waves are managed within the loudspeaker.
- Composites
-
Composite materials are especially useful when strength is needed without significantly increasing weight. They are perfect for enclosures that must be both lightweight and strong, minimizing unwanted vibrations and distortion to optimize acoustic performance.
- Damping Materials
-
Some 3D printing materials possess damping properties, which help absorb unwanted vibrations. This ensures cleaner sound by reducing interference and minimizing resonance.
- Reduced Costs in Small-Batch Production
-
3D printing is especially cost-effective for small production runs and niche products. Unlike traditional manufacturing, which often requires expensive and time-consuming molds or tools, 3D printing eliminates the need for tooling altogether. This allows manufacturers to economically produce limited runs, such as specialized prototypes or custom orders, that would otherwise be impractical.
- Environmental Benefits
-
3D printing, unlike traditional subtractive manufacturing methods, generally wastes less material and can significantly reduce the carbon footprint associated with logistics by enabling on-site production of components instead of relying on shipments from external suppliers. This approach can underscore a company's commitment to sustainability by minimizing waste and decreasing environmental impact while still delivering high-quality products.
The Future of 3D Printing in Loudspeaker Manufacturing
The application of 3D printing technology in loudspeaker development is still growing. As advancements in materials and printing processes progress, we can expect to see increasingly sophisticated applications that enable higher performance and more innovative speaker designs. Companies leading these innovations utilize 3D printing to stay competitive in a rapidly evolving industry.
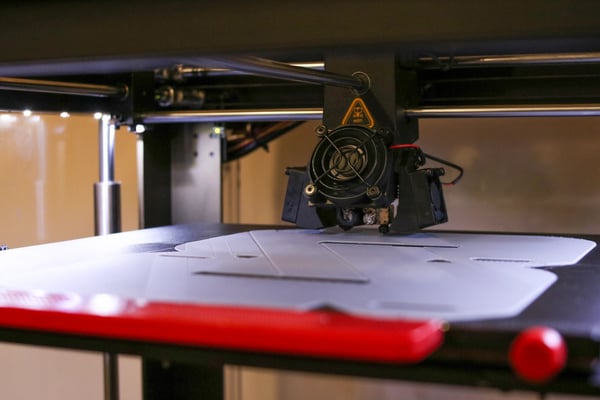
Partnering with Experts for High-Performance Loudspeaker Solutions
Finding the right audio solutions requires a partner with deep expertise and extensive experience. With over 75 years in the industry, MISCO has unparalleled knowledge in designing and producing high-quality, reliable loudspeaker systems.
MISCO provides comprehensive engineering services and conducts rigorous testing throughout the design process to ensure reliability. Our strict end-of-line testing guarantees that each component meets our high standards. Additionally, we offer a complete catalog of off-the-shelf solutions to help save time and resources without compromising performance.
If you're looking for a trusted partner to develop high-quality loudspeaker solutions, contact MISCO today. Our team is ready to assist you in finding the best solution to meet your project's unique needs.