Science Behind the Sound: How We Build Critical Audio Solutions
When your product's success depends on audio quality, the manufacturing process becomes as crucial as the design itself. Engineering teams in various industries need customized audio solutions for applications where consistency and reliability can't fail.
Zach Wilson, MISCO's Production Manager, oversees our advanced manufacturing capabilities. With Zach’s guidance, we manufacture our speakers with precision, ensuring flawless performance in demanding applications.
Reliability and consistency aren’t optional. Here’s how we make them happen.
Responsive Scheduling: Meeting Timelines
Loudspeaker manufacturing relies on consistent production and delivery. Our responsive scheduling system anticipates changes and adapts without compromising quality. Wilson attributes this to his team’s order-to-order philosophy.
"We build-to-order rather than to-stock," explains Wilson. "This way, we can efficiently produce customers’ custom products. If an order suddenly requires earlier delivery, we adjust our schedule to accommodate it without impacting others."
Custom manufacturing allows us to meet specialized requirements without disrupting production flow. Customers with ongoing needs can use stocking agreements to maintain specified inventory levels and blanket order programs for scheduled releases. And when urgent deadlines arise, customers can choose expedited shipping options, including air freight, to receive their order on time without sacrificing quality.
Paperless Manufacturing: Precision Through Digital Integration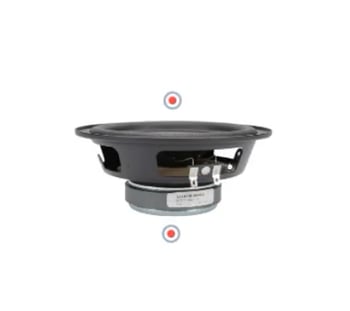
To accelerate our manufacturing (and get speakers to our clients faster), we run product and part data through a digital platform. Work instructions and engineering updates are instantly accessible at every station, eliminating miscommunication and delays. High-resolution product images provide visual guidance during assembly, and automated labor tracking enables real-time efficiency analysis.
"If an engineer suddenly needs to change something on the speaker, they can change it before the line is running or while the line is running, and it will automatically pop up for the assemblers," Wilson explains.
Specialized Production Lines: Custom Needs
Different applications require different approaches. To align with various industry needs, specifications, and certifications, we structure our production facilities with four specialized lines:
- Line One: Dedicated to speakers up to five inches
- Line Two: Focused on speakers five inches and above
- Line Three: Custom builds for aerospace, military, and specialized applications
- Value Add Line: Complete system assembly, including enclosures and lead sets
Each line is optimized for its specific purpose. Whether you need a single prototype or thousands of units, MISCO’s team can adapt. And that level of precision extends to final testing before the product is shipped:
"The very last thing that we do is a 100% inspection, whether it be SoundCheck or just a rub and buzz or a frequency test, just to make sure that we're putting out a quality product," Wilson adds.
Robotic Precision: Enhancing Human Expertise
At MISCO, we use five robotic systems to accelerate production. These robots aren’t meant to replace the expertise of our technicians–they’re intended to speed up production without sacrificing quality or succumbing to labor struggles.
"While we are excitedly moving forward with robotics, it is not replacing our people." Wilson explains, "It's addressing the work shortages that have happened. Robotics is just another resource, kind of like a drill press or anything like that."
Our robots handle everything from pre-assembly of baskets and front plates to full assembly of micro speakers for specialized applications (and we’re the only U.S. manufacturer developing those micro speakers domestically).
They also include camera-based inspection systems–not just to catch a bad part, but to prevent further parts from misalignment.
"If the robots end up having a bad quality problem, it's not just going to keep running thinking everything's okay," Wilson notes. "It'll stop immediately at this point and then alert somebody to focus on it and take a look at it."
Lean Manufacturing: Continuous Improvement
At MISCO, continuous improvement is ingrained in our culture. Our lean manufacturing approach, driven by Kanban inventory management and 5S principles, minimizes waste while maximizing quality.
From Wilson’s perspective, that philosophy has internal and external value.
"Lean manufacturing is part of our quality goal," Wilson states. "Making sure that we're improving every day and eliminating waste. We're not just going to just keep making scrap and throwing it out because that's just going to end up driving up costs for everyone."
Your Partner in Precision Audio
Choosing MISCO means more than just high-quality loudspeakers. It means gaining a manufacturing partner that provides direct access to technical expertise, rapid response to design updates, compliance with industry certifications, and scalable production from prototype to full-scale manufacturing.
We build speakers for products where audio quality matters. Where reliability isn't optional. Where your reputation depends on getting it right.
Learn more about why OEMs choose MISCO for their audio needs.