Revitalizing U.S. Defense Manufacturing: MISCO’s Strategic Investments in Automation and Resilient Supply Chains
The aerospace and defense industries are navigating a complex era marked by heightened demand and significant operational challenges. Geopolitical tensions, regional conflicts, and the need to support allied nations have driven an unprecedented surge in demand for military equipment, including advanced communication systems. At the same time, manufacturers face persistent hurdles such as tariffs, labor shortages, and supply chain disruptions. These challenges are further compounded by stringent compliance requirements like MILSPEC standards, DFARS regulations, and ITAR restrictions, which necessitate secure and traceable supply chains sourced from approved countries.
In this demanding environment, defense manufacturers must adopt innovative strategies to maintain operational readiness while meeting evolving regulatory and market expectations. MISCO has embraced this challenge as a U.S.-based leader in audio solutions for military applications by investing in automation, collaborative robotics, and domestic manufacturing capabilities. These strategic initiatives were implemented to address the financial and logistical pressures of tariffs and align with the defense sector’s increasing emphasis on secure, U.S.-based production.
The Challenges of Tariffs and Supply Chain Vulnerabilities
One of the most pressing challenges confronting U.S. manufacturers is the impact of tariffs on imported components. Since their introduction under Section 301 in 2018, tariffs on Chinese-origin goods have reshaped trade dynamics, often with unintended consequences for industries reliant on global supply chains. For defense manufacturers, critical components such as magnets, semiconductors, and other raw materials face import duties as high as 25%, while fully assembled products manufactured overseas are taxed at lower rates, sometimes as little as 7.5%. This phenomenon, known as “tariff inversion,” creates a cost disadvantage for domestic production and inadvertently incentivizes offshoring.
However, the current tariff landscape has evolved. Since early April 2025, the total tariffs on importing finished speakers from China have reached as high as 152.5%, and 170% on speaker components, making the difference between the 25% tariff on parts and the 7.5% on finished goods less significant in relative terms. This high tariff environment has shifted incentives, making domestic production with parts sourced domestically or from low-tariff countries more attractive.
These tariff fluctuations exacerbate broader vulnerabilities in global supply chains. Many specialized components essential for the construction of loudspeakers, such as voice coils or precision-engineered baskets, are concentrated in a single region, like China. While this clustering has historically offered efficiency advantages, it also creates significant risks during geopolitical or logistical disruptions. Recent export bans on legacy semiconductors have further highlighted these risks, restricting access to chips vital for secure communications and radar systems.
Labor shortages add another layer of complexity. While MISCO has not experienced significant labor shortages specific to defense manufacturing, broad labor shortages persist across the industry. This reality has driven the adoption of automation to enhance productivity and expand capacity without relying on fluctuating labor markets, which would otherwise risk operational readiness.
MISCO’s Commitment to Domestic Manufacturing and Automation
In the face of these challenges, MISCO has taken decisive steps to build resilience into its operations. By investing in automation, collaborative robotics (cobots), and domestic manufacturing capabilities, MISCO has positioned itself to counteract the effects of tariffs while addressing broader supply chain vulnerabilities.
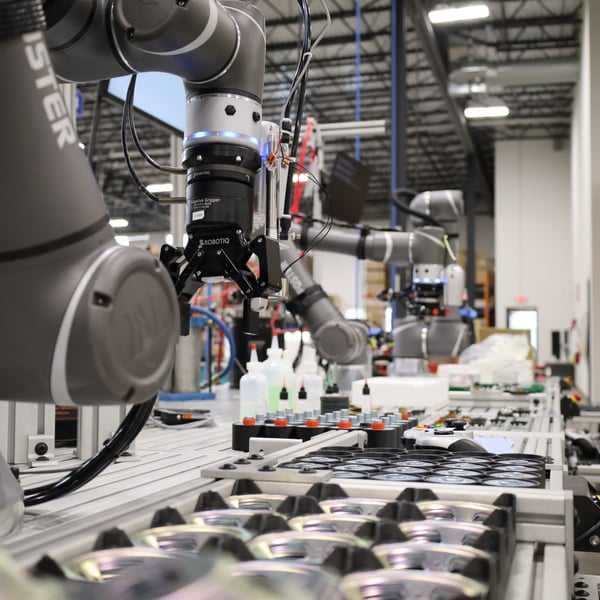
Cobots are central to MISCO’s reshoring strategy. At its Energy Park facility in St. Paul, Minnesota, the company has established cobot-assisted, domestic production of micro-speakers, a process that has historically been performed offshore due to lower labor costs and, until now, was not considered cost effective in the United States. These advanced technologies enable precision manufacturing with consistent quality while significantly reducing labor costs. Automation also enhances adaptability by allowing rapid customization to meet evolving customer needs, a critical capability for defense contractors operating under tight deadlines and stringent specifications.
MISCO’s Minnesota facility is equipped with North America’s most advanced Klippel acoustical testing laboratory and environmental chambers that simulate battlefield conditions. These investments ensure that every product meets rigorous MILSPEC standards while adhering to ISO9001:2015 quality requirements.
Diversifying Supply Chains for Resilience
Recognizing the risks posed by over-reliance on any single region or supplier base, MISCO has diversified its supply chain relationships across multiple regions, including Vietnam, Taiwan, Indonesia, the Philippines, Europe, and North America. The COVID-19 pandemic underscored the importance of having supply chains close to the next step in the process and reinforced the need for diversification. MISCO’s approach to risk mitigation includes setting up reliable supply chains for customers, providing consistent and dependable sources even during global disruptions. This diversification extends beyond final assembly to encompass the entire component ecosystem — a strategic move that enhances flexibility during regional disruptions while maintaining consistent quality across operations.
MISCO’s dual-location manufacturing model exemplifies this approach. About half of its products are produced at its Minnesota facility, which specializes in sophisticated applications requiring engineering support and specialized assembly. The remainder is manufactured through its Asian operations and partners, which focus on higher-volume production where cost pressures are more intense. This model not only provides built-in redundancy but also ensures that production can be matched to customer locations for efficiency.
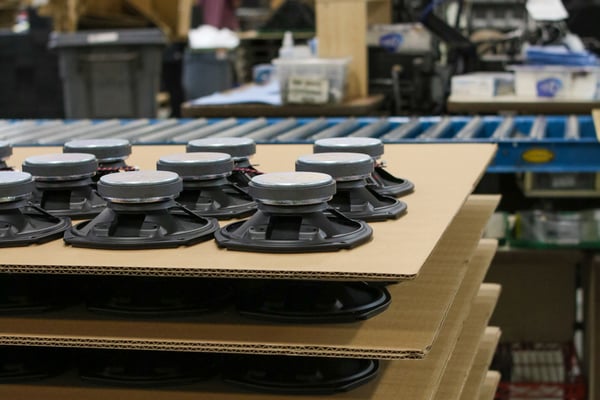
MISCO’s supplier selection process is influenced by a range of metrics, including supplier evaluation scores for quality and financial stability, as well as commercial considerations such as lead times, shipping costs, and labor market conditions. While risks and labor shortages are difficult to quantify, they are factored into overall evaluations. MISCO manages its supply chain by choosing two or three reliable partners for each product type, balancing cost reduction with risk mitigation. This internal diversification strategy, which includes dual sourcing and using the same component suppliers for both U.S. and Asian factories, ensures backup and stability if disruptions occur.
Supporting Defense Contractors With Secure Supply Chains
The defense sector increasingly prioritizes suppliers who align with "Buy American" mandates and Trade Agreements Act (TAA) requirements. By managing its entire production process domestically for critical applications while maintaining diversified global operations for commercial products, MISCO addresses these priorities effectively. Its domestic framework ensures ITAR compliance — a non-negotiable requirement for military applications — and provides traceability for mission-critical products.
Traceability is especially critical for space programs and military applications, where failure risks necessitate deep reviews down to the origin of materials. While domestic manufacturing helps avoid compliance issues, some raw materials, such as magnets, cannot currently be sourced from American suppliers due to environmental and economic considerations. In these cases, MISCO prioritizes vendors who can meet stringent traceability requirements within their supply chains.
Moreover, MISCO maintains quality assurance through the use of sophisticated end-of-line loudspeaker test systems, which measure distortion, frequency response, and other key parameters. Data from these tests is recorded and shared across facilities, ensuring consistency and enabling rapid response to any issues. This rigorous approach is vital for long-term military products, where consistency and reliability are paramount.
A Blueprint for the Future of U.S. Manufacturing
As global trade dynamics continue to evolve unpredictably, balancing cost efficiency with resilience remains a pressing challenge for manufacturers across industries. MISCO’s strategic investments in automation, collaborative robotics, domestic manufacturing capabilities, and supply chain diversification offer a model for navigating these complexities effectively.
By leveraging advanced technologies to offset labor costs, prioritizing quality consistency through rigorous testing protocols, diversifying supplier relationships across regions, and maintaining visibility throughout its operations, MISCO exemplifies how U.S.-based manufacturers can adapt to shifting market conditions while supporting national security priorities.