MISCO’s Integrated Approach to Speaker Testing and Measurement: Unmatched Technology Under One Roof
The development of high-performance loudspeakers requires a blend of art and science, demanding both aesthetic sensibility and exacting technical standards. Within our 70,000 square-foot facility in St. Paul, Minnesota, MISCO ensures that every speaker undergoes comprehensive development from concept to production, a rarity in an industry typically fragmented across multiple locations.
One significant turning point in our company's technological capabilities was the acquisition of Warkwyn by MISCO in 2015. As North America's most comprehensive R&D audio lab at the time, Warkwyn brought exclusive North American distribution rights to the Klippel suite of world-class electro-acoustic analysis instruments, as well as Microflown's particle velocity sensors and CESVA's vibration measurement systems.
By eliminating dependence on third-party testing labs, this acquisition not only created a closed-loop development process where designs move seamlessly from concept to testing to production. It also transformed MISCO into an end-to-end audio engineering powerhouse with testing capabilities previously unavailable under a single roof in the United States.
Comprehensive Measurement and Simulation: From Microscopic Analysis to Real-World Performance
At the core of this engineering process lies a sophisticated measurement and simulation workflow that begins with microscopic analysis and extends to real-world performance prediction:
Laser Vibrometry: Visualizing the Invisible
The Klippel scanning vibrometer serves as the foundation of MISCO's testing methodology, capturing submicron-level vibrations across speaker components. By directing laser beams at up to 3,000 discrete points on a speaker cone during frequency sweeps (20-20,000 Hz), engineers create detailed three-dimensional reconstructions of diaphragm movement. This high-resolution data reveals subtle material and manufacturing inconsistencies that might otherwise manifest as audio distortion or dropouts.
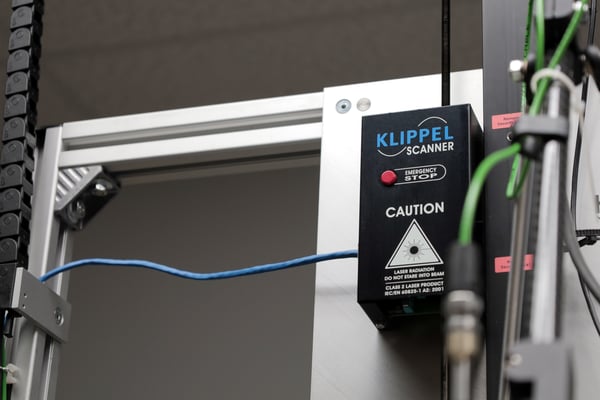
The technology proves particularly valuable when comparing different materials, such as paper versus aluminum cones, each with unique vibrational characteristics. When localized anomalies are detected, such as rippling or asymmetrical movement at higher frequencies, engineers can trace these imbalances to their root causes before advancing to prototype development.
Near Field Scanning: From Component Analysis to Environmental Simulation
Building on this component-level data, MISCO employs the Klippel Near Field Scanner (NFS) to evaluate complete speaker systems. This robotic apparatus collects acoustic measurements from 2,000-3,000 points arranged in a spherical configuration around the speaker, capturing its full three-dimensional sound field. This automated process, which once required weeks of manual testing in anechoic chambers, now completes within hours.
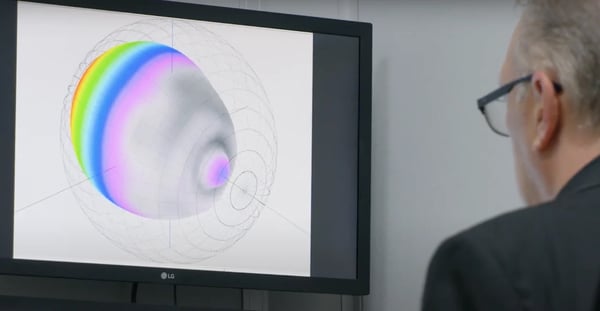
The resulting point-cloud data enables engineers to:
- Visualize how sound radiates in all directions
- Model performance in various environments (automotive interiors, auditoriums)
- Predict acoustic behavior before physical prototyping
- Identify and resolve anomalies that traditional testing might miss
This simulation capability significantly improves design decisions, supports iterative refinement, and minimizes late-stage revisions that would otherwise increase costs or delay launches.
Redefining the Standard for Quality and Precision
The true power of MISCO's approach lies in integrating these advanced technologies into a standardized workflow that spans from initial testing to final production. Rather than isolated capabilities, the laser-scanning vibrometry, Klippel simulation tools, and standardized testing protocols function as an interconnected system that addresses potential issues at their source.
Every MISCO product undergoes comprehensive end-of-line testing, well beyond typical industry “rub and buzz” tests, including measurements of impedance, distortion (total, second, and third harmonics), resonant frequency, quality factor, and polarity. By mirroring these R&D-level test systems across all production facilities, MISCO ensures that every unit, whether manufactured in Minnesota or overseas, meets identical standards. This global consistency creates confidence in the uniformity and reliability of MISCO speakers, particularly critical for demanding applications in military, automotive, and professional audio environments.
The result is a streamlined process that enhances intellectual property protection, accelerates development timelines, and delivers products that consistently meet the most demanding specifications across diverse applications.