Why Rigorous End-of-Line Testing Matters for Your Loudspeakers
Ensuring the reliability of a loudspeaker is essential. But how can you be certain that a loudspeaker is truly dependable? Once a loudspeaker design has been finalized and production begins, manufacturers typically perform end-of-line or end-of-production-line testing before packaging and shipping each unit. However, the methods and thoroughness of these tests can vary significantly between manufacturers.
How Does End-of-Line Testing Work in Loudspeaker Production?
A loudspeaker might sound flawless during a brief audition, but only through thorough and objective end-of-line testing can one determine if the approved design is consistently delivered across all units. Whether the loudspeakers are intended for voice applications, high-end professional audio, or consumer products, customers should reasonably expect consistent quality from unit to unit, batch to batch, and, for long-life products, even year to year.
Some loudspeaker manufacturers apply only a brief single-tone test, colloquially known as the rub-and-buzz test, to their final products. In this test, an operator listens to the sound produced and decides whether the loudspeaker should be shipped. The rub-and-buzz test is primarily used to detect audio defects caused by issues such as an off-center loudspeaker cone, loose particles within the magnetic gap, or excess glue in the assembly. While rub-and-buzz testing is critical and should be performed on each loudspeaker before release, it only verifies that the unit is not audibly defective at that moment. It represents a minimal performance standard that only partially ensures the loudspeaker performs correctly.
Seven Tests for Great Loudspeakers
Once loudspeakers reach the end of the production line, they should undergo a meticulous quantitative testing process. This process ensures that each important parameter of loudspeaker quality is met and that the production batch yields statistically desirable results. These seven end-of-line tests go far beyond simple one-second sweeps and should include:
- Frequency Response Margin
-
Every loudspeaker design has a specific frequency response curve. In production, each unit's frequency response should fall within a defined tolerance window consistent with the driver's intended purpose. Unplanned peaks or dips in the response need to be identified, and any loudspeaker exhibiting these anomalies should be marked as a failure.
- Total Harmonic Distortion Margin
-
Total Harmonic Distortion (THD), also known as the distortion factor, is determined by the ratio of harmonic components to the fundamental frequency. High distortion can be difficult to hear during a short test but is easily measurable. If undetected, it can cause an unpleasant listening experience or, in voice applications, harm critical intelligibility.
- Rub-and-Buzz Test
-
Severe rub-and-buzz issues are easily detected in a quick test, but some high-order harmonic noises, which are less noticeable, should also be measured. Catching them is crucial since they can indicate reliability problems and potential loudspeaker failure.
- Impedance Margin
-
The impedance curve is essential since it is one of the primary performance parameters. Curves outside the margin can reveal issues with voice coil wire, loudspeaker stiffness, moving mass, or inductance changes that may impact other components in the loudspeaker system.
- Average Sensitivity
-
Sensitivity ratings for loudspeakers measure the amount of acoustic output generated per unit of power—that is, how loud they are. Measuring sensitivity is one of the most essential assessments, as it results from motor strength, impedance, and moving mass. A loudspeaker with low sensitivity can cause enormous problems for the end-user, who may need to compensate with higher power, potentially resulting in damage.
- Resonant Frequency
-
The resonant frequency is one of the most basic parameters of a loudspeaker and often determines its use—whether as a woofer, midrange, or tweeter. If the resonant frequency is out of spec, it can throw off the tonal balance of the entire audio system. In a woofer, it can cause a tuning mismatch with the enclosure, which was designed based on an expected resonant frequency.
- Polarity Testing
-
Proper polarity ensures that the wiring has been installed correctly. Multiple loudspeakers that are out of phase with each other can cause low-frequency phase cancellation and ruin the sound quality of the entire audio system. Ensuring correct polarity is crucial for optimal performance in multi-driver audio systems.
Why End-of-Line Testing Is Crucial
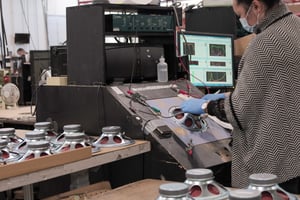
Speakers can be a significant investment and play a critical role in an end-user's experience with a product. An end-of-line test that only covers a single parameter can lead to defects going unnoticed and result in a loudspeaker that isn't usable, wasting money and time for both the customer and manufacturer.
Before purchasing any loudspeaker, it's crucial to understand the rigor of the manufacturer's testing processes. You should be able to request quality control records of each loudspeaker's test results during the manufacturer's end-of-line testing. Your project deserves robust quality assurance procedures and equipment; as a customer, you can demand and ensure this.
Manufacturers Should Deliver Consistent High-Quality Loudspeakers
While end-of-line testing confirms that a loudspeaker meets the expected performance criteria, achieving these standards is only possible through careful design and assembly by skilled professionals. MISCO is known for meticulous end-of-line tests and high standards for passable products. We engineer loudspeakers using high-quality materials so they can reliably function in any unique application our customers require—whether that's in the depths of the ocean or floating in space.
Are you looking for a loudspeaker manufacturer for your next project? Contact MISCO, and we can help you succeed with both custom and off-the-shelf solutions.